Manufacturer's Instructions for Use (IFU) for Disinfection Products in Healthcare
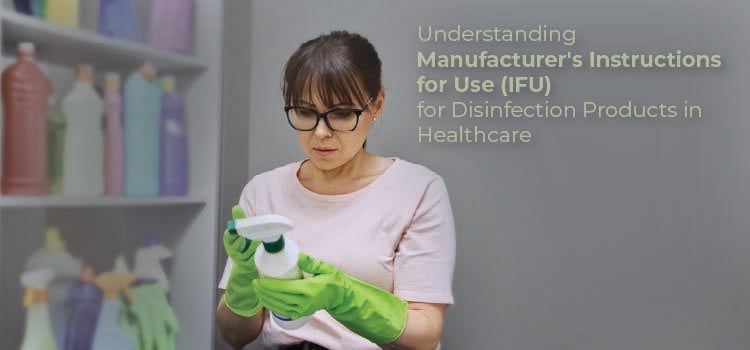
In healthcare settings, cleanliness and infection control are paramount to ensuring the safety of both patients and healthcare workers. The role of disinfection products—whether surface cleaners, hand sanitizers, or disinfectant wipes—is crucial in preventing the spread of healthcare-associated infections (HAIs). However, even the most effective disinfectants can only perform as intended if they are used correctly. That’s where Manufacturer's Instructions for Use (IFU) come in.
IFUs provide the critical guidance needed to ensure that products are used properly, safely, and effectively. Here's a closer look at what IFUs are, how they are created, and why they are indispensable in the healthcare environment.
What Are Manufacturer’s Instructions for Use (IFU)?
Manufacturer’s Instructions for Use (IFU) are documents provided by the manufacturer of a product, detailing the correct procedures for its use. For disinfection products in healthcare, these instructions explain how to properly apply the product, the required contact time (how long the surface or hands must stay wet), and any necessary precautions or safety instructions.
In healthcare, IFUs serve not only to guide proper use but also to ensure compliance with legal and regulatory standards. These instructions often contain important details like:
-
Preparation Instructions: How to mix or dilute the disinfectant, if applicable.
-
Application Method: Spray, wipe, or other methods for applying the product.
-
Contact Time: How long the disinfectant should remain on the surface to be effective against a set range of pathogens.
-
Safety Warnings: Potential hazards like chemical irritants, proper ventilation requirements, or protective gear needed.
-
Storage and Disposal: Guidelines on how to store and dispose of the product safely.
How Are IFUs Created?
The process of creating IFUs is a collaborative effort involving various teams within a manufacturing company. Here are the key steps in developing these essential documents:
-
Product Development and Testing: Before writing the IFU, the manufacturer conducts rigorous testing on the disinfection product to assess its effectiveness against various pathogens, the necessary application procedures, and safety precautions. The results of these tests provide critical data for the IFU.
-
Collaboration with Regulatory Experts: Manufacturers work with regulatory experts to ensure that the IFU complies with national and international standards, like those set by the Environmental Protection Agency (EPA) in the U.S. for disinfectants, or the European Medicines Agency (EMA) in Europe. These regulations dictate the types of information that must be included and the language that must be used.
-
Legal Considerations: Manufacturers must also consult with legal teams to ensure that the IFU is clear, accurate, and protective of both the company and users. This helps mitigate potential liability if the product is misused or fails to meet expectations.
-
Ongoing Updates: IFUs are not static documents. As new research emerges or regulations change, manufacturers are required to update their instructions to reflect the latest best practices. For example, the COVID-19 pandemic has led to revisions in cleaning and disinfecting guidelines, prompting updates to many IFUs.
How Are IFUs Regulated?
In healthcare, the use of disinfectants is heavily regulated to ensure safety and efficacy. Here are some key regulatory bodies involved in overseeing the creation and distribution of IFUs for disinfectants:
-
Environmental Protection Agency (EPA): In the U.S., the EPA regulates disinfectants as part of its responsibility for protecting human health and the environment. The EPA ensures that the claims made in the IFU (such as the product’s ability to kill specific pathogens) are supported by scientific evidence and testing.
-
Food and Drug Administration (FDA): The FDA is involved in regulating certain disinfectant products, particularly those used in medical devices or healthcare settings that may come into direct contact with patients.
-
Occupational Safety and Health Administration (OSHA): While OSHA primarily oversees workplace safety, it also plays a role in ensuring that disinfection products are used safely in environments like hospitals, where chemical exposure can pose health risks to workers.
Who Writes the IFUs?
Typically, the manufacturer is responsible for creating and writing the IFU. This process often involves multiple departments:
-
Product Development Teams: They provide technical information on the product's formulation and application.
-
Regulatory Affairs Specialists: These experts ensure that the IFU meets all legal and regulatory standards and guidelines.
-
Medical and Scientific Experts: They ensure that the information provided in the IFU is accurate, particularly regarding efficacy and safety.
-
Legal Teams: They help ensure that the document shields the manufacturer from liability while clearly communicating safety instructions.
Why Are IFUs Important in Healthcare?
IFUs are crucial for several reasons, especially when it comes to disinfection products in healthcare:
-
Ensuring Efficacy: Disinfection products are designed to kill harmful pathogens, but they can only work if used properly. Incorrect application can result in ineffective disinfection, potentially leading to outbreaks of healthcare-associated infections (HAIs).
-
Ensuring Safety: Disinfectants often contain chemicals that can be hazardous to both patients and healthcare workers. IFUs provide important safety information to help prevent accidents, such as skin irritation, respiratory issues, or exposure to toxic substances.
-
Legal Compliance: Disinfection products must meet regulatory standards for both effectiveness and safety. IFUs help demonstrate compliance with these standards, reducing legal risk for healthcare facilities and product manufacturers.
-
Training and Consistency: In a healthcare setting, multiple staff members may be using the same disinfection products. Clear and consistent instructions help ensure that everyone follows the correct procedure, which is vital for maintaining cleanliness and infection control.
-
Minimizing Errors: Healthcare environments are fast-paced and can be chaotic. Having clear, well-written IFUs reduces the risk of errors, ensuring that healthcare workers don’t miss important steps in the disinfection process.
Manufacturer's Instructions for Use (IFU) are not just a legal formality—they are a vital component of ensuring that disinfection products are used effectively and safely in healthcare settings. By following the detailed instructions provided by manufacturers, healthcare facilities can minimize the risk of infection, protect their staff, and ensure patient safety. Unfortunately, IFUs are not always followed perfectly, meaning that some pathogens are not being killed. This is why biocidal surfaces, including copper-infused EOScu, can be a vital safety net for healthcare facilities, continuously killing disease-causing pathogens even when human error occurs.
If you are involved in the procurement or use of disinfection products in a healthcare setting, make sure to familiarize yourself with the IFUs. It could be the difference between a safe, clean environment and the potential spread of harmful pathogens.