Infection Control and the Healthcare Supply Chain: Who Makes Decisions?
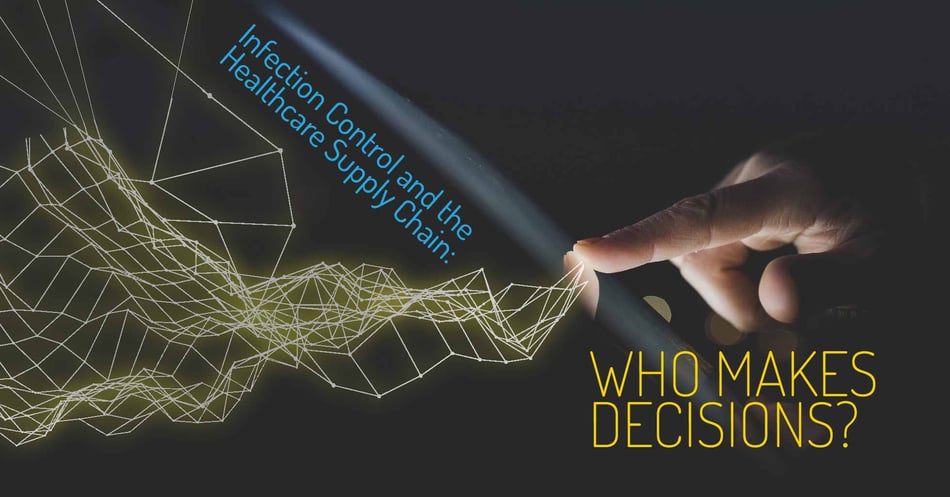
Last week we provided a big-picture overview of the healthcare supply chain, from supplier to patient. This week, we will dig deeper into this process and try to identify places along the supply chain where decisions can impact infection control and prevention. While all hospitals must meet EPA- and FDA-mandated standards for cleanliness and device protocols, there is room for individual choices in how each facility will prepare and respond to pathogens. So where along supply chain are decisions made that influence infection control?
Group Purchasing Organizations
One of the first places many people might think decisions are made about infection control along the supply chain is with group purchasing organizations, or GPOs. Actually, GPOs do not choose or even buy products, they simply negotiate contracts with manufacturers and distributors. The benefits are realized 1) if the hospital is a member of that GPO and 2) if the hospital chooses one of the member vendors. GPOs have resulted in a savings of up to $55 billion a year in the US, or 10-18% on products and services. Where the choice comes in is with membership to a GPO. 97% of hospitals have an affiliated GPO, that is, a single GPO through which they order many supplies. They can still order outside of the GPO, however, and this is where choice comes in. If the facility discovers a product that they want to try, but is not included in their group purchasing agreement, they can purchase it independently.
Hospital Procurement Process
The decisions about products from hand sanitizer to MRI machines are handled through each facility's procurement process. Choosing the product is just one step of many, which can include a purchasing agent, who places the orders, to a clinical team, who approves new products, or a department head, who wants a new product evaluated. The ordering process can present a challenge to a clinician who learns about a new product and believes their facility would benefit from it. A strong relationship with their administration as well as a vendor who is willing to attend multiple meetings can make a dedicated clinician more successful. In the procurement process, a hospital benefits from listening to clinicians and including them in the process so that choices can be made to improve patient outcomes, including infection control and prevention.
External Factors
The move to value-based purchasing (VBA) has impacted how hospitals select products. Because VBA incentivizes positive patient outcomes and experiences (quality over quantity), hospitals have shifted their ordering practices to support this new model. As a result, some facilities may now have a greater emphasis on reducing hospital-associated infections, as they directly impact VBA. HAIs join other adverse events (falls, bed sores, prescription errors, for example) as "non-price motivators" for hospital purchasing departments. The bottom line is no longer enough.
Automation has also transformed hospital supply choice. With ordering going digital, purchasers have simple and accessible platforms from which they can quickly place orders and monitor supplies. Adding a new product that is not included in this automation can mean delays to implementation if facilities do not have a process in place for integrating new or trial products. Clinicians who want to try out a new product need to know their facility has ways of integrating innovative products into their arsenal, and purchasing agents need to be prepared to accommodate their requests. Additionally, vendors need to be sensitive to a facility's many external and internal financial pressures, and be flexible, transparent, and available.
In an ideal world, a clinician would learn about a new product, press a button, and have a supply ready to implement immediately. While this instantaneous adoption process is not realistic, there is significant work being done to make the ordering process and supply chain smoother to navigate. Clinicians in infection control and prevention, whose success is measured in non-events, are helped by the recent focus on preventable adverse events. but even they have a challenging road ahead. Clinicians are at the forefront of their fields, learning about new products almost daily, so it behooves everyone to get out of their way and let them get what they need to help their patients. Financial and administrative constraints are inevitable - and an essential part of reining in healthcare spending - but they should not be insurmountable.
Are you debating whether to bring preventive biocidal surfaces to facility but don't quite know where to start? Click below for some ideas from our Education Team.